Innovations In Thermoforming: Shaping The Future Of Manufacturing
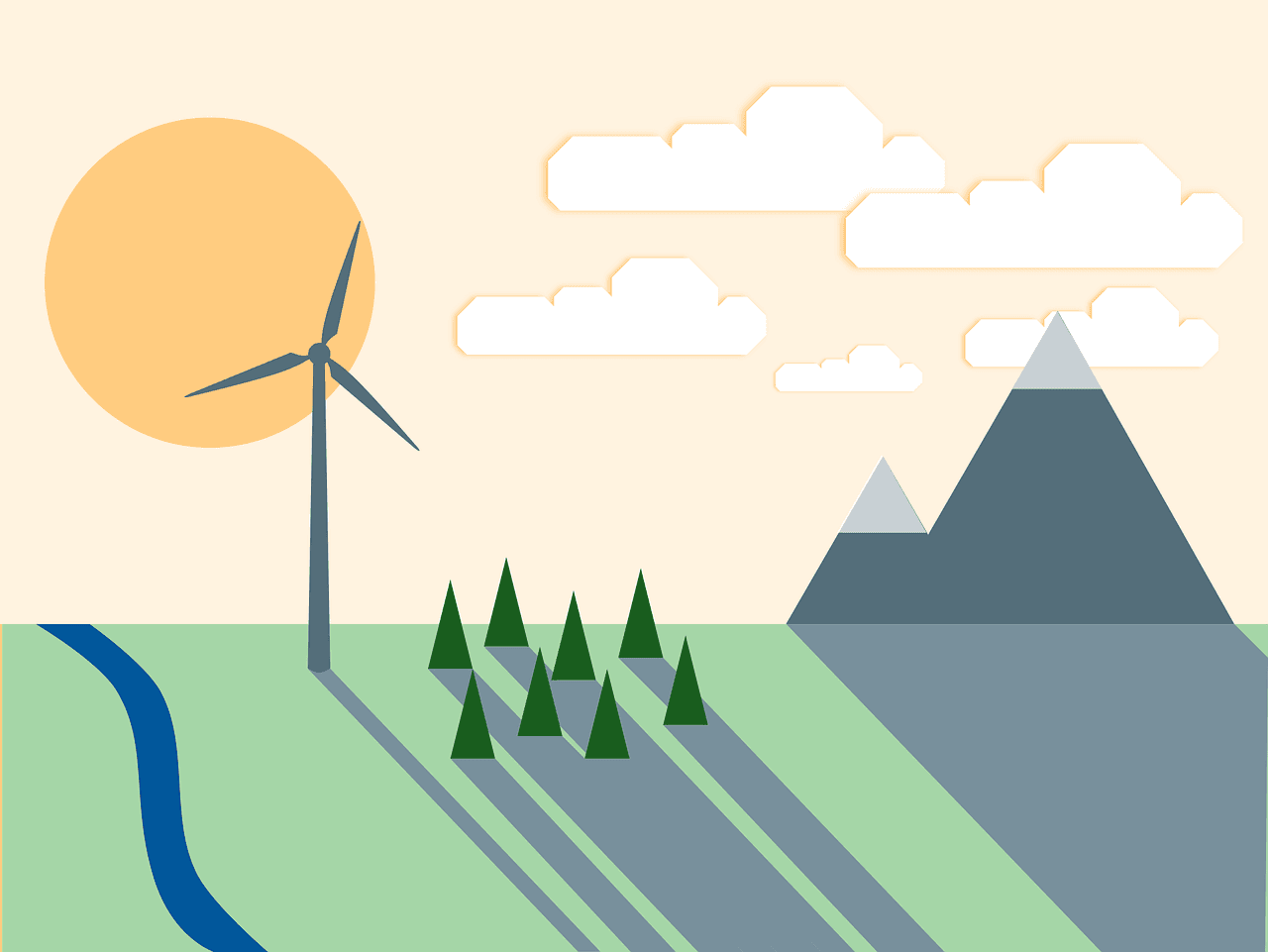
Photo by Marc Manhart from Pixabay
The manufacturing landscape constantly evolves, driven by technological advancements and innovative approaches. One such development at the forefront is thermoforming. This article delves into the latest innovations in thermoforming, revealing how these breakthroughs are revolutionising the way products are created and impacting various industries.
This may interest you: Innovation Is Everyone’s Business
Understanding Thermoforming
Thermoforming is a process that starts with a simple concept: heating plastic until it becomes pliable. Once heated, this malleable plastic is stretched over a mold, taking its shape, and cooled to form a solid structure. This simplicity, however, belies the sophistication behind the process. It offers an unmatched level of versatility, allowing for producing a wide range of items, from intricate medical devices to large automotive parts. The process can handle varying thicknesses of plastic, adapting to the specific needs of different products. Its efficiency stems from the ability to rapidly produce large quantities of items. At the same time, its cost-effectiveness is evident in the minimal waste produced and the low labor costs involved. Thermoforming has become an indispensable tool in modern plastic manufacturing, bridging the gap between conceptual design and mass production.

Recent Technological Advancements
Technological innovations continuously reshape the landscape of thermoforming. In recent years, the field has seen an infusion of advanced software that brings a new level of precision to the thermoforming process. This software lets designers simulate the thermoforming process before production, identifying potential issues and optimising material use. Moreover, automation has been a game-changer. The process has become faster and more consistent by employing robotic arms and automated workflow systems. These advancements have not only improved the quality of the end products but also significantly reduced the environmental footprint of the manufacturing process. Modern thermoforming techniques are setting new standards for efficiency and sustainability by minimising material waste and streamlining production lines.
Integration Of Vacuum Forming Illinois
The application of vacuum forming Illinois exemplifies these innovations' practical and versatile nature. Vacuum forming involves heating a plastic sheet and then using a vacuum to pull it onto a mould, creating precise and intricate shapes. This method is particularly beneficial for producing large, shallow-depth products. It is widely used in industries like automotive manufacturing and packaging. In Illinois, this technology has bolstered local manufacturing capabilities and attracted a diverse range of industries seeking customised, high-quality plastic components. The adoption of vacuum forming in this region is a testament to the adaptability of thermoforming technologies, catering to specific industrial needs while maintaining efficiency and precision.
Sustainability In Thermoforming
Sustainability in thermoforming has moved from a peripheral concern to a central focus in recent years. The industry has shifted towards more environmentally friendly practices, primarily through recycled materials. By incorporating post-consumer plastics into the thermoforming process, manufacturers reduce the demand for virgin materials, thereby lessening the environmental impact. Additionally, the development of biodegradable plastics represents a significant stride towards a more sustainable future. These materials, designed to break down after use, reduce the long-term environmental footprint of plastic products. This shift towards sustainability is not just a response to regulatory pressures; it reflects a growing recognition within the industry of its responsibility to minimise environmental impact while meeting the demands of consumers and businesses.

Listen to this: ESG's Powerful Role in Your Business
Enhancing Material Properties
The realm of material science has been pivotal in elevating thermoforming to new heights. Researchers continuously explore and develop advanced thermoplastic materials, enhancing their strength, durability, and versatility. These innovations have resulted in materials that can withstand extreme temperatures and harsh environments, expanding thermoformed product applications. Lightweight yet robust materials have become particularly valuable in sectors where weight reduction is critical, such as the aerospace and automotive industries. The ability to tailor the properties of these materials to specific application requirements has opened up new possibilities for product design and functionality. This ongoing evolution of material properties does not just enhance the quality and durability of products. Still, it also enables designers and manufacturers to push the boundaries of what can be achieved through thermoforming.
Customisation And Personalisation
The thermoforming industry has embraced the trend towards customisation and personalisation in manufacturing. Advanced digital technologies, such as 3D printing and computer-aided design (CAD), have allowed for greater flexibility in product design, enabling the production of bespoke items tailored to individual specifications. This capability particularly benefits industries requiring unique, made-to-order components, such as medical devices or customised packaging solutions. Small-scale production runs, once economically unfeasible, have become possible and cost-effective. This shift towards customisation is not just meeting the specific demands of clients but is also fostering a more dynamic and responsive manufacturing environment. It allows manufacturers to quickly adapt to changing market trends and customer preferences, ensuring a competitive edge in a rapidly evolving market.
Thermoforming In The Medical Field
The medical industry has witnessed a significant transformation with the adoption of thermoforming. This technology is crucial in creating sterile, precision-engineered trays and containers for medical instruments and supplies. These products require the highest standards of cleanliness and exact specifications, which thermoforming can reliably provide. The ability to produce lightweight yet sturdy and transparent medical packaging has improved the safety and efficiency of medical procedures. Furthermore, thermoforming allows for customising medical trays and enclosures to fit specific instruments, aiding organisation and accessibility during surgeries and other medical processes. This precision and adaptability make thermoforming an indispensable part of medical manufacturing, ensuring that healthcare providers have the tools to deliver effective care.

Impact On The Automotive Industry
The automotive industry has reaped substantial benefits from the advancements in thermoforming. The development of lightweight yet strong materials is particularly advantageous, contributing significantly to vehicles' overall fuel efficiency and performance. Thermoformed components like door panels, dashboards, and trunk liners are integral to modern vehicle design. These parts need to be durable, resistant to wear and tear, and aesthetically pleasing. Thermoforming allows for producing complex shapes and fine details, which are essential in automotive design. The flexibility of this process also supports the industry's move towards more sustainable practices, as it allows for the integration of recycled materials into new components. The impact of thermoforming on the automotive industry underscores its role in driving innovation and efficiency in one of the world's most significant manufacturing sectors.
Future Trends And Predictions
Looking to the future, thermoforming is poised to continue its trajectory of innovation and improvement. Integrating artificial intelligence (AI) and machine learning into the thermoforming process is one of the most exciting prospects. These technologies promise to enhance the precision and efficiency of production, with AI algorithms optimising material usage and production workflows. Machine learning could enable real-time adjustments during manufacturing, reducing errors and improving product quality. Another area of future development is the exploration of new materials and techniques that can further reduce environmental impact and enhance product functionality. The potential for integrating smart technologies into thermoformed products, such as embedded sensors or interactive surfaces, is also a frontier to be explored. These advancements will not only refine the process of thermoforming but also open up new possibilities for product innovation and application.

Read more: Why Responsible AI Use is Good for Business
Challenges And Opportunities
Despite its advancements, the thermoforming industry faces challenges that must be navigated to sustain growth. Managing costs while investing in new technologies and materials is a significant challenge, especially for smaller manufacturers. The rapid pace of technological advancements also challenges staying current and competitive. However, these challenges also present opportunities. For instance, the push towards sustainability can drive innovation in eco-friendly materials and processes, creating new market opportunities. The need to remain competitive can spur manufacturers to adopt more efficient, automated processes, improving productivity and quality. Additionally, the increasing demand for customised and personalised products offers a chance for manufacturers to diversify their offerings and cater to niche markets. The ability to adapt to these challenges and capitalise on the opportunities they present will be key to the continued success and evolution of the thermoforming industry.
Conclusion
Thermoforming is not just shaping plastics but the future of manufacturing. Its innovations offer immense potential to enhance manufacturing processes and contribute to a more sustainable and efficient production landscape. The continual evolution of thermoforming technologies is a testament to human ingenuity and the relentless pursuit of improvement in the manufacturing sector.
Be sure to check out the media below:
Leaderonomics.com is an advertisement-free website. Your continuous support and trust in us allow us to curate, deliver and upkeep the maintenance of our website. When you support us, you enable millions to continue reading for free on our website. Will you give it today? Click here to support us.
Business
Tags: Alignment & Clarity, Artificial Intelligence, Be A Leader, Building Functional Competencies, Business Management, Environmental, Social and Governance (ESG), Sustainability
Oliver Reynolds is a manufacturing enthusiast with a keen interest in innovations in thermoforming. With a background in industrial engineering, Oliver specialises in exploring the latest advancements shaping the future of manufacturing. Beyond his professional pursuits, he enjoys staying informed about emerging technologies, attending manufacturing expos, and volunteering for initiatives that promote sustainable manufacturing practices.