Talent Development (M) Sdn Bhd: Why We Need To Collaborate With Technology
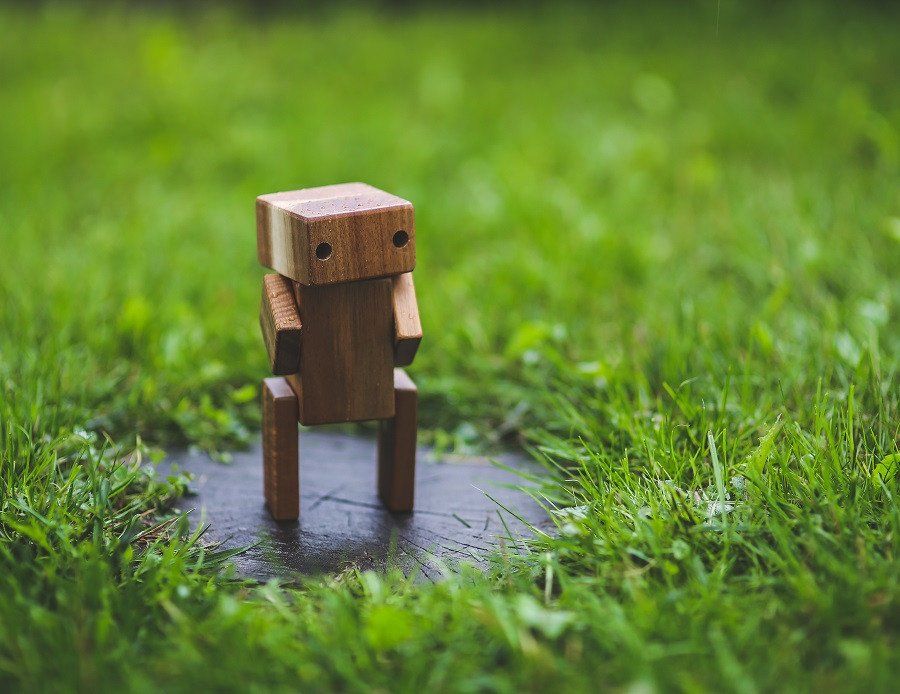
The future of automation and why we should embrace the world of Industry 4.0
Whether it’s the fear-filled rhetoric of conspiracy theorists or the sensationalist dramatisms of popular culture, it is easy to believe that the rise of robots and artificial intelligence will spell the end of human worth in the workplaces of the future. The manufacturing and services sectors in particular are adapting to the “rise of the robots” that takes its hold in an ever-evolving world.
A recent market trend is to believe that the onset of robotics will spell the end of human capital in the workforce altogether.
“Robots don’t take coffee breaks!”
“Robots can work 24/7!”
“Robots don’t have a bad day!”
“Robots aren’t distracted by the latest drama at home!”
“Robots can do a better job in a fraction of the time!”
The above are just samples of some of the sentiments surfacing more and more commonly in the industry today. But Talent Development (M) Sdn Bhd chief operating officer (COO) Prasanna Sailanathan sees things a little differently.
Rather than looking at the onset of the fourth industrial revolution – commonly known as Industry 4.0 – as a threat to future human resource development, Prasanna recognises that these technological advantages give rise to the potential for major upskilling and whole new fields of expertise.
Talent Development (M) Sdn Bhd chief operating officer (COO) Prasanna Sailanathan
“There have been countless times in history during which we thought a certain invention or technological advance would do irreparable damage to our working conditions,” said Prasanna.
“And yet every time this has happened, we have seen a whole new set of opportunities arise from such a change and have adapted accordingly. Industry 4.0 will not be the end of human labour, but it will certainly shed light on the need to upskill. reskill and multi-skill our workers to be able to stay relevant.”
An upskilled worker in the world of Willy Wonka
To put a pop culture spin on it, the opportunities for an upskilled and emphatically relevant human workforce can best be seen in Tim Burton’s unique take on Charlie and the Chocolate Factory.
Early on in the 2005 fantasy movie, the down-on-their-luck Bucket family are further ravaged by the news that protagonist Charlie’s father has lost his job in the manufacturing industry.
Having spent many years working in a toothpaste factory screwing the lids on the tubes in the final seat on the factory line, Bucket’s company realises that a machine would be a more efficient substitute and renders the Bucket patriarch redundant.
Not to mention single-handedly boosting tooth decay worldwide.
Putting aside the zany antics of the remainder of the film, the epilogue offers an uplifting end to Bucket’s story as he later finds a career, repairing the very machine that first took his job at the factory.
Not to say that, in the future, every single factory worker and manufacturing employee needs to learn the art of machine repair, but it nevertheless offers an insightful take into how new working opportunities present themselves with each technological innovation.
“I am sure that in the future, there will be no shortage of people out of work claiming that ‘a robot took my job’,” said Prasanna.
“It’s inevitable. But the people that aren’t willing to learn the skills that a robot could never possibly learn are simply not doing enough to help themselves.
Understanding Industry 4.0
While breaking the complex history of the manufacturing and power-based industries into four distinct eras may seem like a crude oversimplification, the term Industry 4.0 has become a buzzword across the media and business landscape.
Between 1760 and 1840, the ‘industrial revolution’ changed the way in which manufacturing was changed forever.
The textile industry brought about the most significant change by moving production from hand-made designs to more machinery-based methods. The increased use of steam power, water power and the factory system also became hallmarks of the overhaul.
When the second industrial revolution hit towards the end of the nineteenth century, increased connectivity through improved railroad networks and the invention of electrical power and telephones made production even easier and propelled the world into the next stage of human development.
The term ‘globalisation’ entered the lexicon and hitherto unfathomable technologies rocked the foundation of society.
The ‘digital revolution’ – beginning in the late 1950s (or 1970s depending on who you ask) – saw the invention of computers and, later, the Internet, bring about an even greater speed of life.
Where centuries before, messages were sent around the world in bottles carried on ships, now the possibility of email and instant messaging had connected the world further. The state of numerous industries changed along with these developments.
In today’s world, the introduction of ‘smart’ devices, cloud-based storage systems, ‘big data’ and human-mechanical interfaces are largely pinpointed as the quintessential components of the fourth industrial revolution, with global connectivity more essential than ever.
As Prasanna tells it: “I can be typing away at my computer here in Kuala Lumpur, which is programming and sending commands to machines and devices in New York, Mumbai and Cape Town simultaneously. This is the value of the cloud, gone are the days when a worker would need to be standing next to a machine pulling a lever. This technology i called remote trouble shooting, remote diagnostics and remote learning.”
“As with any of the industrial revolutions before now, the future of industries will be clearly broken down into those who understand these technologies and the opportunities they present and those that are stuck behind the times.”
Bridging skill gaps in the 21st century
Talent Development has spent many years already preparing the Malaysian workforce for these impending challenges.
As the first private training centre in Malaysia and Asean to offer the Siemens Mechatronic System Certification Program (Level 1), Talent Development has been upskilling, reskilling and multi-skilling workers in the technology and engineering fields. Their offerings include Siemens Industry Training programmes that are customised to suit industry needs.
Talent Development is also the only MAERSK-authorised training provider – in the country and Asean – to deliver oil and gas and maritime training programmes. With their labs being IoT compatible and ready to be digitised, Talent Development is doing excellent work in helping Malaysia achieve its goal of being recognised as a high-income nation by the year 2020.
As she oversees the current Malaysian workforce staying ahead of the curve, Prasanna has a unique first-person perspective on what needs to be done in order to embrace Industry 4.0. This all starts with seeing the future as an exciting and interconnected world in which anything is possible, rather than a career-limiting automation-dominated landscape.
“Many of the job titles and positions we will see in the future, we can’t even imagine now,” she continued.
“But it is important to be able to see the bigger picture of what an exciting time humanity is on the cusp of here. We will always feel that technology is one step ahead of us, but it will force us to constantly be evolving, relearning and never stopping to rest on our laurels. I think that’s incredibly exciting.”
To find out more about how you can upskill your existing workforce or yourself in order to meet the demands of Industry 4.0, visit www.talentdevelopment.my for a full listing of the courses offered and more tips on how to evolve with the times.