How Will Ergonomics Change With Industry 4.0?
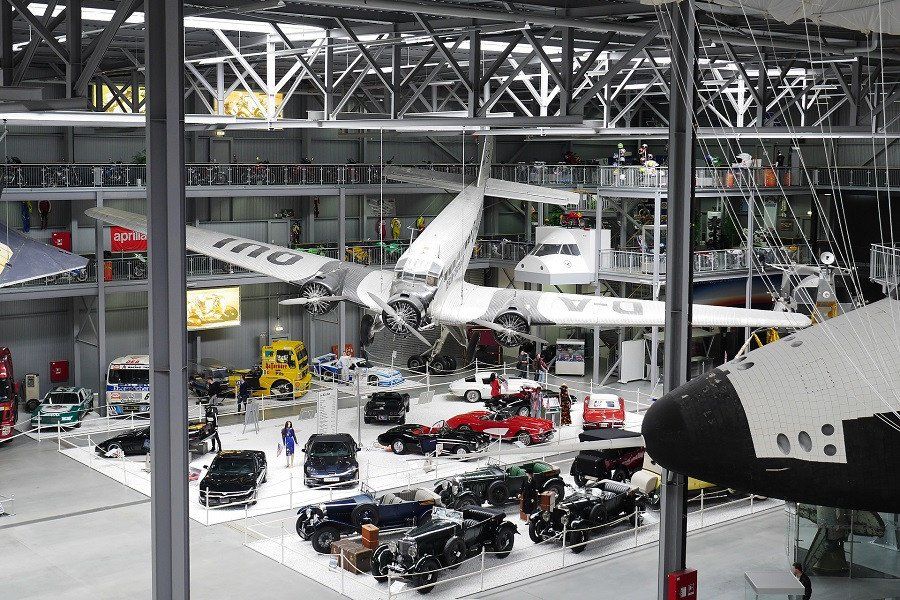
With the emergence of smart factories, smart cars, smart homes and smart what-have-you, are we smart enough to relook our ergonomics design?
I became familiar with the term “ergonomics” when one of the subjects I took as a Computer Science undergraduate was human-computer interaction. Those were the days when our mobile phones weren’t really that ‘smart’, so our assignments included redesigning the device.
According to International Ergonomics Association, ergonomics is the science of designing machines, products and systems to maximise the safety, comfort and efficiency of the people who use them. That means the collaboration between humans and machines should operate as one unit.
Today, with internet of things (IoT), machine-to-machine (M2M), big data, cloud computing, immersive simulation, augmented reality, robotics, smart factory and additive manufacturing becoming the buzzwords of Industry 4.0, how is ergonomics changing with times?
One size doesn’t fit all
How everyone functions in relation to a system can be unpredictable because humans don’t come in one-size-fits-all configurations. We are built differently in terms of proportion, ability and strength.
For example, the workplace design of an automotive plant that works well in Europe may need some tweaking to suit the working environment and culture if a new plant is to be built here in Asia.
Alas, ergonomic considerations are often an afterthought in the design process. A poor ergonomic design may result in a productivity dip as people learn to adapt to these machines, often uncomfortably, when the integration between humans and machines should be seamless.
Ergonomics going virtual
Industry 4.0 is pushing the boundaries of man by challenging us to rethink the traditional value chain and the way we work through digital lens to help increase productivity and reduce wastage. One way to achieve this is to bridge the gap between the physical world of humans and the digital world (see Figure 1).
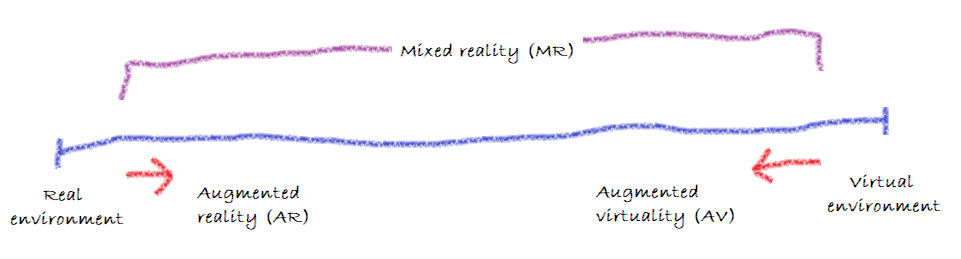
Figure 1: Reality-virtuality (RV) continuum Source: www.Engineering.com
The union between these two worlds has birthed forth what is termed as cyber-physical system, a complicated ‘network of machines, physical contacts, virtual items, computing facilities and storage, communication devices that interact with each other and exploit the enormous potential of new technologies’ (Elena Laudante (2017) Industry 4.0, Innovation and Design. A new approach for ergonomic analysis in manufacturing system, The Design Journal, 20:sup1, S2724-S2734, DOI:10.1080/14606925.2017.1352784).
Recommended for you: Using Virtual Reality To Train The Next Generation
Simulating human interaction with software makes it possible to reduce the need for physical mockups, which can be costly and time-consuming in the work cycle.
While the marriage between both worlds is highly complex, it is possible through invested resources in research and development.
Personal encounter with virtual ergonomics
I was one of the fortunate Malaysians to attend the “Industry 4.0 and Digitalisation Programme for Media” under K-Pintar–ESMT (European School of Management and Technology) in Germany recently to witness how the future of digital transformation is so much closer to reality than I initially thought.
A site visit to Fraunhofer Heinrich Hertz Institute (HHI) opens up a whole new world of virtual reality (VR) where the institute collaborates with various industry players and universities to explore the limitless possibilities of integrating VR into the real world.
It includes new audio and video technology that gives users a realistic impression. For example, Fraunhofer HHI’s Omni-Cam-360 provides an immersive 360° panaromic experience where users feel as if they were attending a live event in a concert hall or sports event.
With their gadgets and displays such as the 3D without Glasses and Interactive 3D Book Explorer, you realise how much thought their researchers have placed in integrating ergonomics and VR.
Championing ergonomics
Countries like Australia strictly observe their work health and safety best practices because of the economic costs behind workplace incidences. In economic terms, the International Labour Organization has estimated that more than 4% of the world’s annual GDP (gross domestic product) is lost as a result of occupational accidents and diseases.
In Malaysia, much needs to be done to further educate employers and the workforce in private and government organisations on the importance of ergonomics. Most of us probably don’t even realise the existence of Human Factors and Ergonomics Society Malaysia (HFEM), a non-profit organisation that champions the cause of ergonomics in this country.
While agencies like HFEM and the Department of Occupational Safety and Health are doing their due diligence to champion ergonomics, there is no time to waste in Industry 4.0 as business leaders with digital leadership skills need to step up to face the challenges of technological advances and organisational contraints such as business models, processes, leadership and culture.
This might interest you: 4 Constraints Preventing Your Organisation From Becoming World-Class
Food for thought
Former Leaderonomics editor Karen Neoh summed it well in her article “The Economics of Ergonomics” that leaders have to commit to taking action to ensure a good working environment for all. Corporate culture and management advisor Brian Fielkow lists out some of his action plans to operationalise wellness in his article, “Weave Health And Wellness Into Your Company’s Culture”. Essentially, leaders are investing into a corporate culture of wellness when they consciously invest in their people’s and wellbeing at the workplace.
With more machines and robotics being integrated in digital manufacturing, how ready are we in preparing our people toward a safer working environment maintaining the machineries of 3D printers?
With constant invasion of real-time application, disruptive technology and IoT in our lives, how are we coping cognitively? With frequent organisational changes, are we doing enough to optimise organisational ergonomics?
These are questions related to ergonomics that we need to look into to transition into the future of work where automation become ubiquitous like in the world of Tron.
How are you preparing your people to advocate good ergonomics design and practise proper working conditions? Write to us at editor@leaderonomics.com. We would love to hear from you!
Functional