4 Ways BIM Helps in Reducing Construction Costs
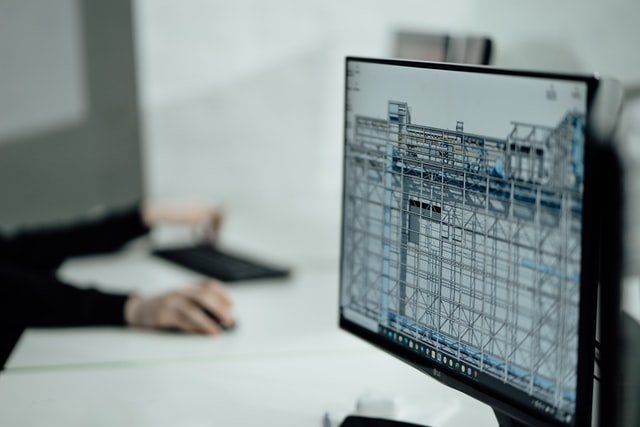
Photo by Evgeniy Surzhan @ unsplash
Disclaimer: The views expressed in this article belong to an independent guest author and not Leaderonomics, its directors, affiliates, or employees.
It’s no secret that construction projects can be quite expensive. After all, they require teams of professionals and workers, large quantities of materials, specialised equipment, and unique skills. They also last for months, sometimes even years, if they are particularly big.
Still, thanks to modern technology, many aspects of design and construction run much smoother than they used to. BIM is particularly well known for improving the construction industry’s overall efficiency, as well as reducing costs. So, let’s take a closer look at this software.
What Is BIM?
Though people often think that Building Information Modeling, or BIM, is just design software, it goes far beyond that. In fact, it is a whole new movement in construction that promotes efficiency and collaboration. To that end, BIM software creates a model containing all the necessary information about a building’s construction and maintenance.
While the model thus created is typically 3D, it contains far more than just basic measurements, floor plans, and spatial positioning. BIM incorporates as much data as possible — for instance, costs, sustainability, project completion time estimates, and light and daylight analyses. Thanks to that, architects and project managers already have a full picture before the building even begins.
Even after the project is complete, the information that BIM provides remains useful. After all, it’s easier to maintain and improve the building when there’s plenty of available information about it than otherwise.
How BIM Reduces Costs
Clearly, BIM and related software make the construction process simpler and more efficient. What’s particularly interesting for project managers, though, is whether it reduces the costs too. And as it happens, that’s one of its primary benefits.
So, how exactly does BIM reduce the costs? Let’s take a look at the following four ways.
1. Improved Collaboration Leads to Fewer Mistakes
If BIM is known for anything, it’s for its effect on team cooperation. Before this software was introduced, all communication had to be done in person or through phone calls and emails. That, of course, had its downsides — namely that it was inefficient and could lead to misunderstandings and mistakes.
For instance, if one person decided to adjust something on the design, they’d have to let everyone else working on it know. Then, they would make the necessary changes too. However, any sort of miscommunication could lead to a mistake that would seriously impact the actual construction process, usually resulting in delays and money loss.
But with BIM, everyone has access to the same software and the same model. Whenever they update something, the whole team can see it and make their own adjustments — or, in advanced versions, the mode automatically changes. Either way, there’s no need for endless emails and phone calls, and collaboration is much smoother.
Thanks to that, mistakes in the final version of the design are far less likely. As a result, there’s no need for changes, delays, and additional expenses.
2. BIM Makes Accurate Cost Estimates
An essential part of each construction project is calculating and predicting exactly how much everything will cost. It’s also extremely difficult to do — after all, there are materials to take into account, safety equipment and measures, salaries, machinery, and various other expenses. Doing it all manually can result in miscalculations and bad budgeting decisions.
But with good BIM software, a computer can take over a large part of that work. The program instantly estimates how much various parts of the project will cost and displays everything clearly. With this information so readily available, it’s not that hard to decide what expenses are too high and if anything can be cut down. In fact, BIM software can let us know if there is any potential for cost reductions.
3. BIM Can Help Us Decide Which Materials to Purchase
When deciding which materials to purchase, it’s important to find a balance between affordability and quality. But that’s far from simple — with so many available options out there, choosing the right one is challenging. Or at least as long as BIM isn’t involved in the process.
When it is, BIM can do all the necessary calculations for us. This software doesn’t only display how much certain material costs, but it can also compare different manufacturers and determine which one is the most cost-effective. Even beyond that, it can alert us to particularly low market prices and notify us when the right time for purchase is. All these things would be too much for one person to do, but the software should have no issue.
With such in-depth information, cutting down on materials costs should no longer be an issue. Then, the money thus saved can be directed elsewhere, making the project more cost-effective overall.
For your enlightenment: Quotable Quotes: Achieving Cost-Effectiveness
4. BIM Gives Us a Preview of the Building
Before BIM, architects and project managers could only see whether their design truly worked once the construction was underway. At that point, if there were any mistakes or issues, they would crop up and need to be fixed. That often included design changes and delays or even undoing the work and starting over. Unsurprisingly, all that invoked additional costs.
But now that BIM exists, it’s much easier to visualise what the final building would look like. That allows architects to spot any issues before they come up and address them. In other words, changes and delays once construction is underway are far less likely to happen.
In Conclusion
BIM has changed almost all aspects of the architecture and construction industries. The projects are completed faster, communication is smoother than ever, and even costs are much lower. On top of that, BIM still hasn’t even reached its full potential. As technology advances further, BIM will receive fantastic upgrades that will make it even better. And we can’t wait to see what it will offer us.
Check out the media below:
Leaderonomics.com is an advertisement free website. Your continuous support and trust in us allow us to curate, deliver and upkeep the maintenance of our website. When you support us, you allow millions to continue reading for free on our website. Will you give it today? Click here to support us.
Business
Tags: Hard Talk, Consultant Corner
This article is published by the editors of Leaderonomics.com with the consent of the guest author.