Health & Safety: People Are Precious!
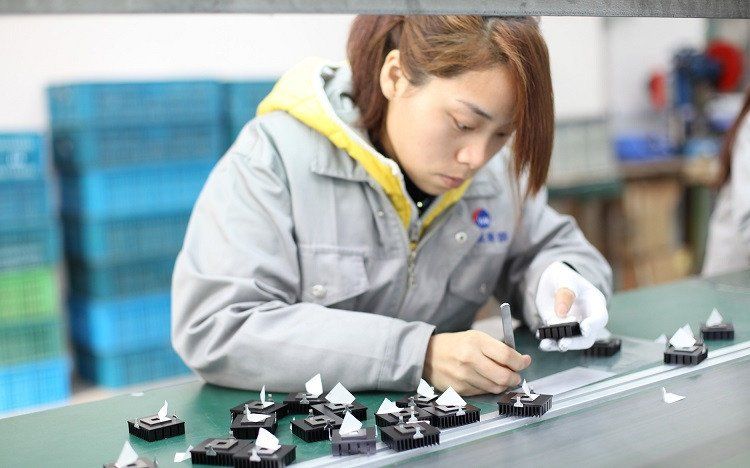
The International Labour Office (ILO) and International Ergonomics Association (IEA) developed the Ergonomic Checkpoints mobile app, which provides best practice recommendations for implementing effective improvements in the workplace.
It also allows users to create interactive checklists of ergonomic checkpoints.
As there are 132 checkpoints, I thought we might share a select few in this instalment – with an emphasis on skilled trades.
For more detailed information on each of the checkpoints, do go to the ILO website.
1. Eliminate tasks that require bending or twisting while handling materials
Why: Bending or twisting of the body is an unstable movement and is one of the major sources of back injuries, and neck and shoulder disorders. We spend more time and become more fatigued than when doing similar work, but without bending or twisting.
Risks/Symptoms
- Muscular strain
- Low-back pain
- Slips, trips or stumbles
- Excessive reach
How
- Change the positions of materials so that the handling work is done in front of us, without having to bend
- Improve the working space so that we can adopt stable foot positions
- Use mechanical means to bring the work items and replace the finished item without being forced into an awkward posture
- Change the working height so that the worker can handle the work item without bending
2. Provide safe power tools and make sure that safety guards are used
Why: Power tools are efficient but usually more dangerous than non-power tools; the greater the energy, the greater the danger. Nevertheless, safe power tools are available. There is no need to use unsafe tools.
Risks/Symptoms
- Amputation
- Hand/finger injury
- Excessive force
- Upper limb disorder
How
- Order power tools only after safety specifications have been examined. Three important points are:
- protection against power transmission and points of operation
- prevention of unintended activation of controls
- easy operation with secured grips
- Purchase tools that have been designed for use with a balance if they are to be used over a fixed workstation
- Check that the guards are sufficient to protect workers, and are used
- Guards should not interfere with work, otherwise people will remove them
- Check if multiple means are used in order to prevent unintended activation of controls
3. Provide a “home” for each tool
Why: If each tool has a “home”, i.e. a special and permanent place allocated to it, workers can find the tool quickly and are encouraged to use the right tool at all times. If tools do not have “homes”, some workers lose time searching for lost tools.
Tools stored in their special places can be seen at a glance. Their inventory is therefore easy, which is a great help for good maintenance.
Risks/Symptoms
- Tool damage
- Slips, trips or stumbles
- Hand/arm injury
How
- There are various means of providing a “home” for each tool. This can be a special shelf, a drawer, a particular place on a rack, an easy-to-see container, a tool trolley, a hook on the wall, suspension from an overhead structure, or a tool board. The most appropriate means should be chosen considering the size, shape and weight of the tool.
- Do not forget to find a “home” also for bigger tools. Avoid the practice of putting large tools on the floor
- When various small tools are used, provide a tool storage board or special containers in which each tool has its own “home”.
- In the case of a tool board, the outline of each tool could be drawn to show where it goes. Alternatively, labels could be used.
- The more frequently a tool is used, the closer its “home” should be to the worksite.
Related article: Ergonomic Checkpoints
For more Consulting Corner articles, click here. Drop us a line or two in the comment box provided, or write to us at editor@leaderonomics.com.
First appeared on Leaderonomics.com. Published in English daily The Star, Malaysia, 27 June 2015
Functional